As the world’s capacity to cope with the fast rising manufacturing of throwaway plastic items overwhelms the world’s ability to deal with them, plastic pollution has become one of the most important environmental challenges. Plastic pollution has become a major issue in the developing countries of Asia and Africa.
But the so-called developed countries are not too safe from future disasters. In one week, the United States alone wastes away enough plastic bottles to round our globe five times! That’s just 5% of the world’s population. Approximately 160,000 plastic bags are used
worldwide, every second.
Every country from around the world is making a stand to use less and less plastic in their daily life with an approach towards 100%
recycling of the materials.
Waste plastic delivered to landfills is the most visible kind of pollution linked with plastic packaging. Plastics are highly stable and hence remain in the environment for a long time after they are discarded, particularly if they are buried in landfills and hidden from direct
sunlight.
To address this ever-increasing challenge, every government is now adopting a recycling strategy. But recycling can’t resist
the ever-growing production of plastic. During production of plastic an enormous amount of carbon and other toxic gasses are released. Nonetheless, the data revealed that the majority of harmful discharges were released into the atmosphere, with the plastics sector
accounting for 14% of the national total and it seems that production of the material is going down in the near future as With an average annual output of 360 million tonnes, plastic manufacture in the first 10 years of this century surpassed that of the previous century.
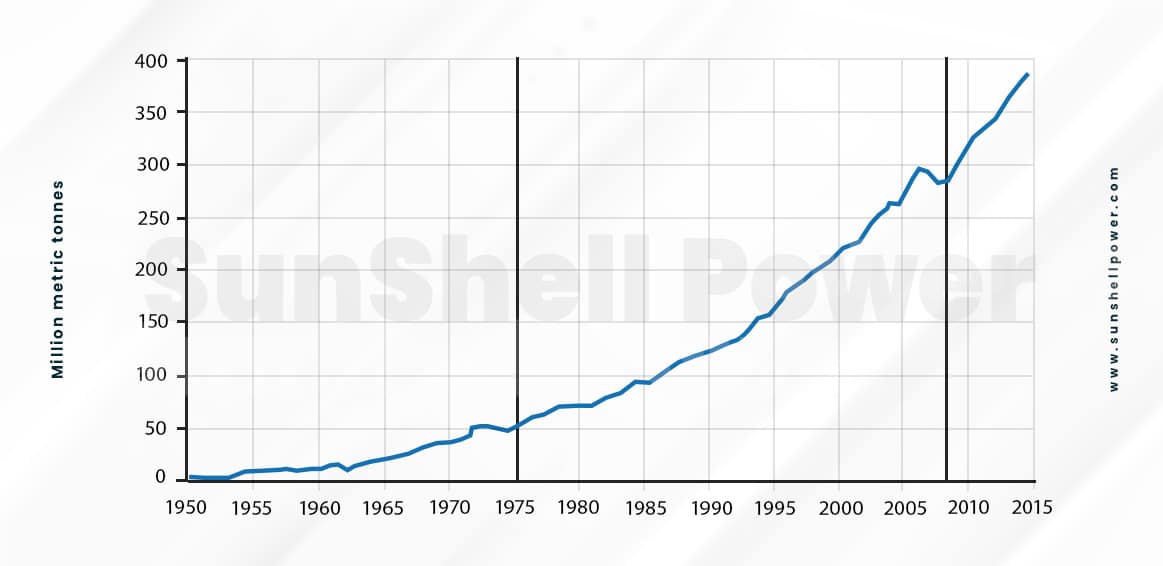
As plastic has become a core part of our everyday life, replacing it with some other options seems to be very difficult and costly, as, apart from being easily available plastic is also very pocket-friendly.
In India, there are approximately 15 large scaled polymer manufacturers, with approximately 30,000 plastic processing units, producing an estimated 5.58 million tonnes with a waste of 3.4 million tonnes in the FY 2021-22.
In 2020, the worldwide plastic market was estimated at $580 billion US dollars, while India’s plastic raw material export industry was valued at $353.04 million US dollars in July 2021. Inonly one month, exports totaled roughly 1.57 billion dollars and the industry is expected to grow at a CAGR of 8-10 % till 2025.
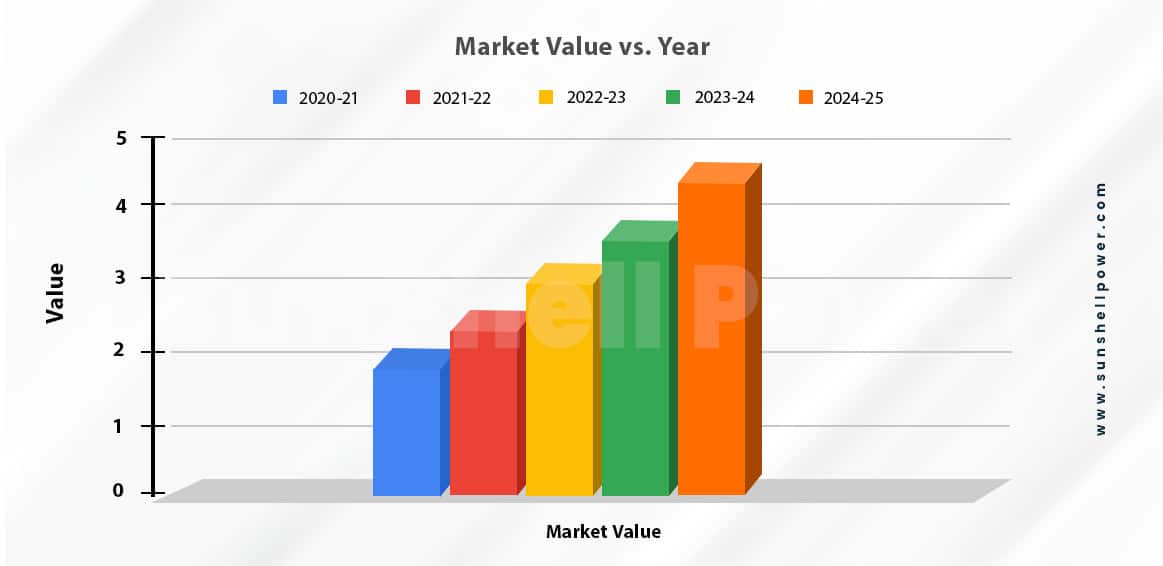
Now to look deep into the plastic production industry and the market scenario, we first need to know how plastic is being produced at an
industrial scale.
Components & Working Process of a Plastic Factory:
Natural gas, oil, or plants that have been converted to ethane and propane are used to make plastic.
Plastic is classified as either synthetic’ or ‘biobased.’ Crude oil, natural gas, and coal are used to make synthetic polymers. Biobased
plastics, on the other hand, are made from renewable materials such as carbohydrates, flour, vegetables, fats and oils, microorganisms,
and other biological materials.
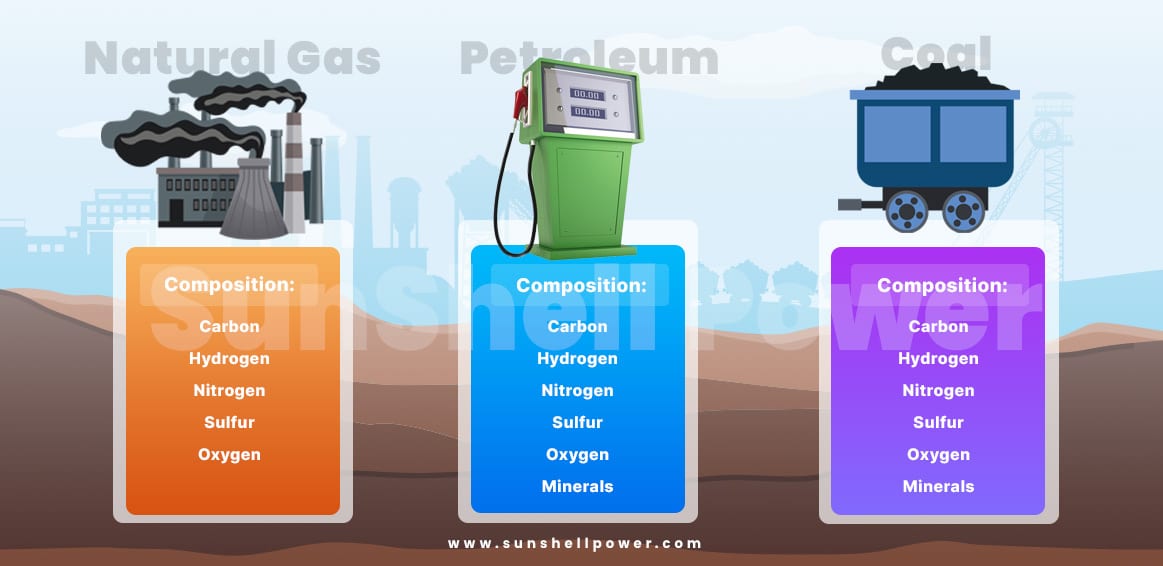
- Procurement of Raw Materials : The majority of the plastics used today have crude oil as their main raw material. But natural gas, coal are also procured from facilities as raw materials.
- Refining The Raw Material : The crude oil is sent to the pre-heater which then boils the crude oil and then is sent to the furnace. During the recycling process we get Lubricating Oil, Diesel Oil, kerosine, petrol & gasoline, naphtha and petroleum gas etc. Here Naphtha is the one of the main products for producing plastic.
The substances are kept in different container units where Ethene is the main component for making plastic. Ethene is made from
Naphtha. - Producing Ethene: To produce Ethene, Naphtha is sent to the Naphtha Cracking Center , where Naphtha is heated upto 800℃ by using steam crackers. In the quenching process Naphtha is broken down into hydrocarbons then it is compressed and refined we get Ethene Propylene Butane, petroleum,Ether etc. By this process we made our important product in plastic production that is Ethene.
- Conversion into Polythene : Ethene is converted into polythene by the process of polymerization. Polymerisation is a process in which light olefin gasses such as ethylene, propylene, and butylene (monomers) are transformed into higher molecular weight hydrocarbons in the petroleum industry (polymers). When monomers are chemically linked into chains, this occurs. Polymerization occurs via two main methods.
Basically there are two different mechanisms for polymerisation. - Addition Polymerisation : When one monomer joins to the next (dimer), dimer to the next (trimer), and so on, this is known as the addition polymerisation process. This is accomplished by using a catalyst, usually peroxide. Chain growth polymers are the result of this process, which adds one monomer unit at a time. Polyethylene, polystyrene, and polyvinyl chloride are examples of additional polymers.
- Condensation Polymerisation : Condensation polymerisation is the process of connecting two or more monomers by removing tiny
molecules like water. The reaction between neighboring monomers also necessitates the use of a catalyst. Because you may, for example, join an existing chain to another chain, this is known as step growth. Polyester and nylon are two examples of condensation polymers.
First the Ethene is compressed and cooled then it is now dense almost like liquid. Then it is sent to the reaction chamber. In the reaction chamber initiators which are used to start a chain reaction are added. These initiators kick start polymerization in which Ethene is
converted into polythene. The polythene is then sent to a chamber that adds antioxidants and stabilizers. - Making of Polythene Strings: Then the extruder converts polythene into polythene strings. These strings are passed through the grinder which converts these strings into polythene pellets. These pellets are then sent to various industrial production units like bottle
manufacturing, glass manufacturing and bag production etc. Extrusion or a different molding process then transforms these pellets into a finished or a semi-finished product.
Compounding is usually done on a twin-screw extruder, where the pellets are processed into plastic items with distinctive designs,
diverse sizes, shapes, and colors, as well as precise qualities, according to the processing machine’s predefined settings.
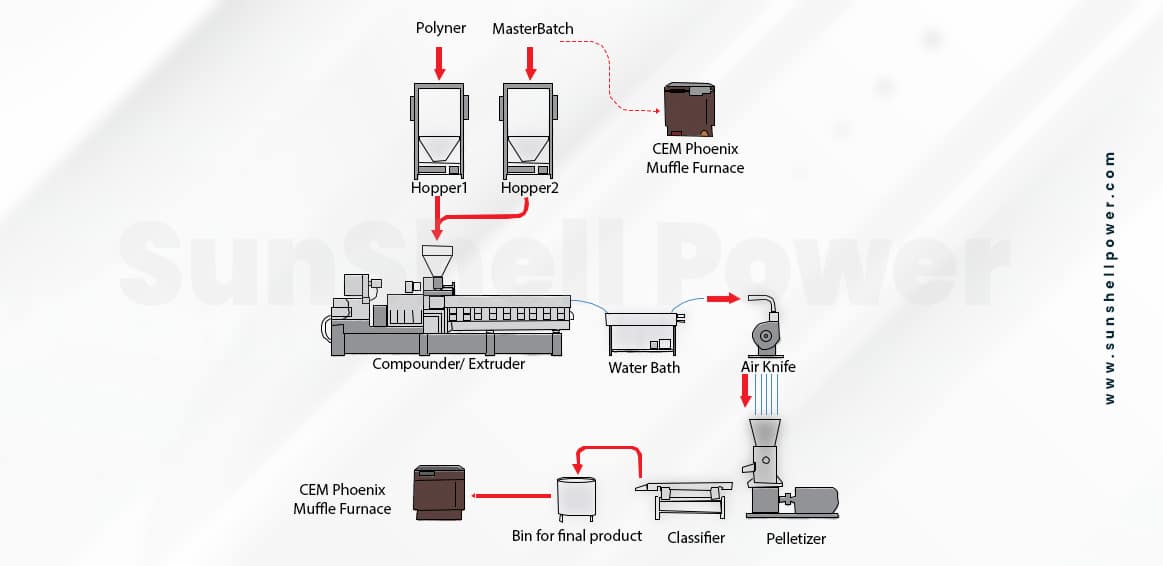
Electrical Load:
The electrical load of a plastic processing plant solely depends on the production capacity and type of
monomer used in the facility.
In plastics production, 100% run time is always the aim, which is why so much effort is put into maintaining the plant’s equipment and
infrastructure.
The worldwide electricity need for plastic production was estimated to be 160TWh .
In injection molding process the extruder motor’s Specific Energy Consumption (SEC) can be upto 0.3288 kWh/ kg. The average
electrical consumption of production of 1 kg of plastic is around 1.47 kWh .
Even though these numbers can vary as the electrical consumption fully depends on the molding process and can have a range from 0.9 to 1.6 kWh/ kg.
So, for a plastic plant to be operational for 24 hours , a solar power plant of size 100 kWp is needed.
Problems faced by Plastic Factories:
As a result, the plastic industry, which has been dubbed the “primary concern” for the approaching gray world, is dealing with both
internal and external problems.
- Unreliable Power Leading Towards Disaster : As majority of the machineries used in the plastic processing units are needed to be active throughout the whole day, dropdown in voltage and power outage can lead to wastage of raw materials and impact on the quality of the finished products.
- Plastic, The Leader In Pollution Parade : Increased demand and the industry’s post-COVID recovery implies more waste, which
producers have attempted to mitigate to varied degrees over the previous decade.
More plastic production automatically leads towards more pollution, as plastic is one of the major reasons behind increased pollution and while production of 1kg of plastic emits around 1.52 kg of CO2. So,using grid power to produce plastic is constantly increasing the carbon footprint of our country and planet. - More Diesel More Cost : As majority of the processing units use Diesel as their main backup source of power and as the power cut and power fluctuation is a quite common thing, high diesel costs lead to more operational expense for these plants.
- Higher Tariff Charges : The big industrial consumers like steel factories, cement plants , dairy product processing plants, plastic
processing units draw a lot of power. As the tariff charges are rising day by day, the energy cost also rises accordingly.
So, What’s The Way Out ? Solarizing Plastic Factories
As the plastic industry has already been one of the main reasons behind global pollution and global warming, the least this industry can do is to produce the plastic by green energy and increase the recycling percentage even more by the next 5 years.
Human civilization is increasingly moving towards renewable energy as technology advances. Solar power plants are the most dependable energy source among renewables. Solar modules have a 35-year life expectancy and need no maintenance, making the plant a stable power source.
For plastic processing farms, we offer four types of rooftop solutions :
- Grid-connected Solar Rooftop Plant,
- Solar Submersible Pump,
- Solar Street Light,
- Energy Efficiency
Grid-connected Solar Rooftop Plant (On-Grid) :
Solar energy system that is grid-connected and accessible through net metering, as well as a credit system based on power banking. This kind of power plant is ideal for businesses with a high demand for electricity and few power disruptions.
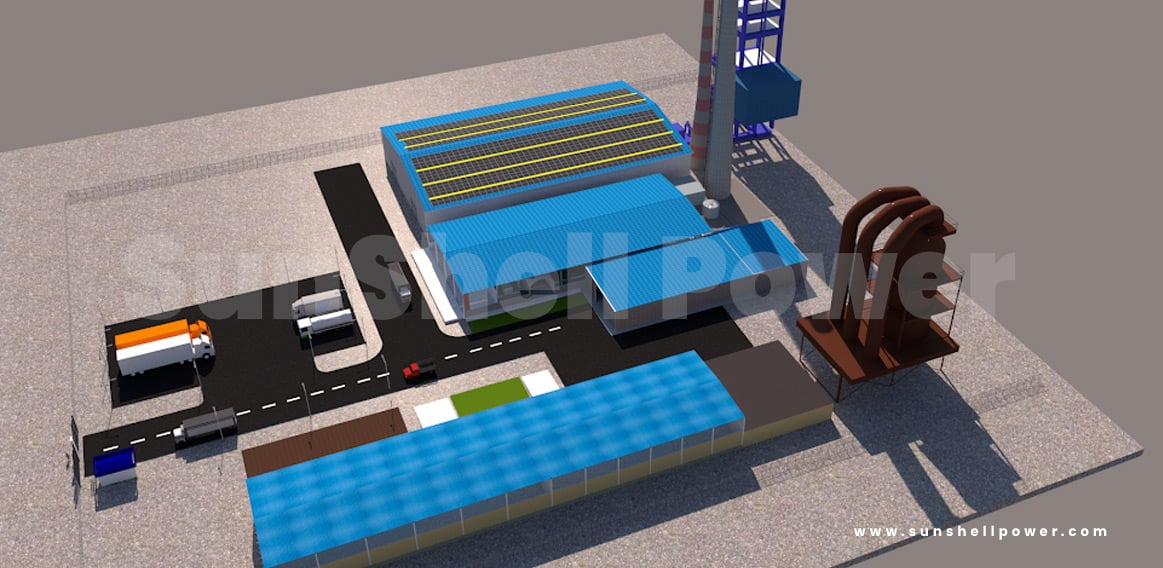
Why On-Grid ?
Even though in SunShell Power, every solar power plant is important and valuable for us, for plastic processing plants we would highly
recommend the authority to install on-grid solar power plants. From our previous experiences, and customer testimonials we have pointed out several points from which we have declared the Grid-connected plant to be a clear winner:
- These systems are ideally suited for very high power usage and for lowering energy expenditures
- On-grid plants can be installed with or without net-metering
- On-grid systems are very cost-effective and easy to install
- As there is no battery backup in the system, there are less chances of battery failure and hence the maintenance is minimal which can be helpful in the busy environment of the plastic processing unit.
Benefits of Installing Solar in Plastic Factory:
Now, the question remains, why should I invest in solar & what are the benefits that the other options can’t provide ?
Apart from being eco-friendly and producing green energy, solar power plants are a great financial and economical investment, which is also a reliable source of power. Here, from the feedback of our previous consumers we have listed overall benefits of solar,
- Reduced electricity bills as dependency on conventional electricity & DG is reduced
- Government gives subsidy for solar panel installations
- Tax benefits upto 40% by going for accelerated depreciations
- Low maintenance and average life-span of 25 years
- Environment friendly solar power plant is the best way to preserve and make the planet greener
- Proper utilization of the blank space on the roof shades
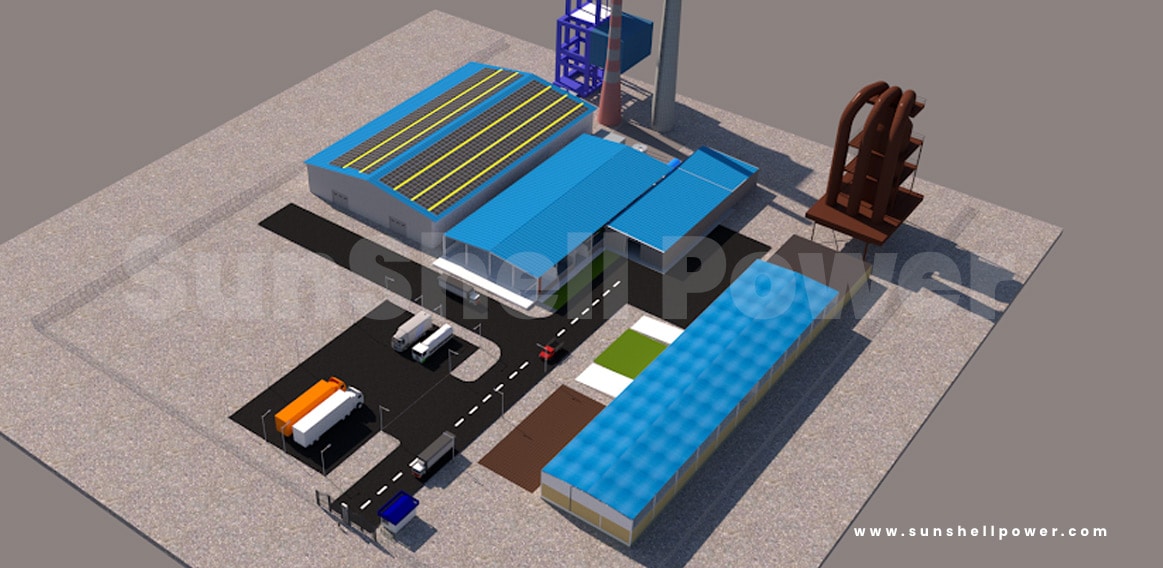
Average ROI :
The average ROI of a grid-connected solar plant in a dairy processing unit is around 3.5-4.5 years, it can change based on the load of the facility.
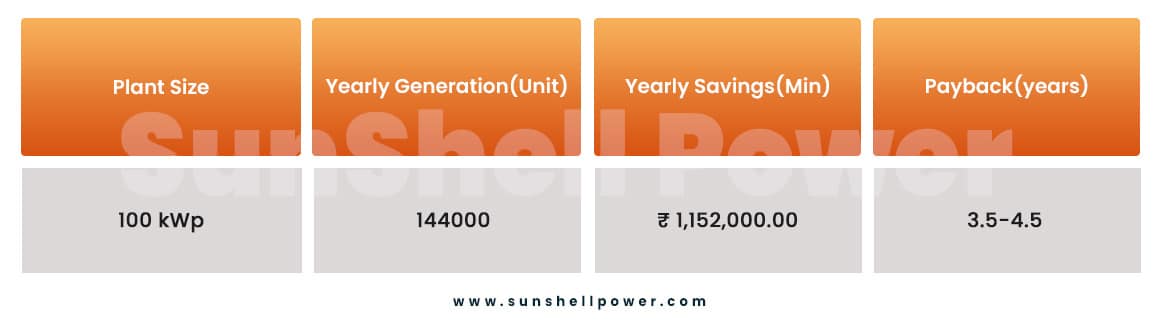
Solar Submersible Pump :
As in plastic processing plants, reserved water is required during the Naphtha production step, regular supply of water is required for this continuous process. Solar submersible pump is ideal for pumping water from underground to cater to such purposes.
Solar Street Lights :
As plastic being a highly flammable material, plastic processing units require regular monitoring of the premises. So proper illumination during the night time is required for safety and inspection purposes of the product. Solar street lights are the exactly right product for this purpose. We ,at SunShell Power, would suggest two types of solar street lights for the facilities.
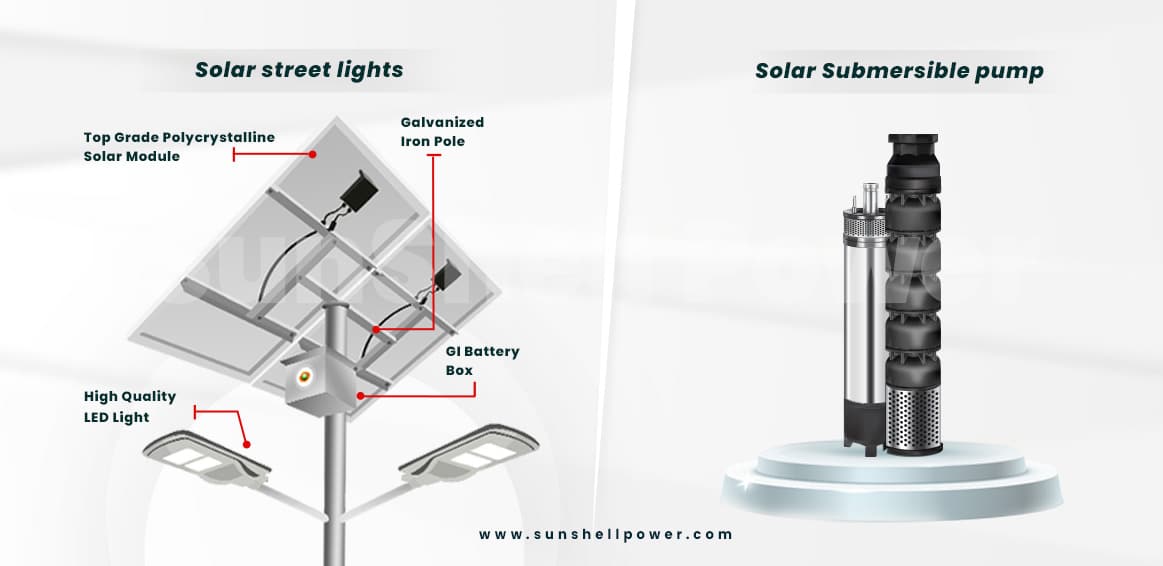
- Two-in-one (Semi-integrated) : Used for a variety of purposes, these are easy to install and are low-maintenance.
- Solar Mini Mast: Best for places with unstable power sources. It uses green energy and needs almost negligible maintenance.
Energy Efficiency :
As per to meet the required upcoming demand in the country and to scale the export business of this sector, energy efficiency and management of waste heat is equally important.
Energy Audit :
Energy auditing is an energy assessment. This assessment looks at how energy flows through a structure, process, or system in order to minimize energy input while preserving or increasing human comfort, health, and safety.
According to the definition of ISO 50002 standard, an energy audit is a systematic analysis of energy use and energy consumption within a defined energy audit scope, in order to identify, quantify and report on the opportunities for improved energy performance.
There are three types of energy audits:
According to the definition of ISO 50002 standard, an energy audit is a systematic analysis of energy use and energy consumption within a defined energy audit scope, in order to identify, quantify and report on the opportunities for improved energy performance.
There are three types of energy audits:
- Walk-Through Audit,
- Energy Diagnosis,
- Investment Grade Audit
Depending on the purpose and potential savings the type of energy audit is chosen.
If the priority is to identify potential savings and further studies a walk-through audit is recommended whereas if the intention is to invest a large amount of money in energy efficiency measurement an Investment Grade Audit is done.
Benefits :
- Energy auditing helps reduce costs in the facility,
- It helps reduce environmental damage and pollution,
- If any energy is active then it can be detected.
Inclination Towards A Green Future :
As the world leads towards the net-zero target, India has also set a target of net-zero by the year 2070. Govt. are offering various schemes and policies for solar installations.
Alpha Rho, an injection molder of rigid plastic boxes of various sizes has decided to go solar. According to President David Tall, the firm will generate more than 80% of its electricity needs to operate its production, storage, and administrative activities. Due to the 36,000 sq. foot roof-space of the facility, the company has been able to install approximately a 238 kWp plant.
The plastic manufacturing sector must come forward to cater to the world’s ever rising carbon emissions.
Enquire Now